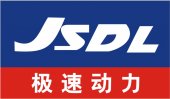
四川極速動(dòng)力超微粉體設(shè)備制造有限公司
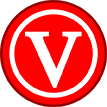
已認(rèn)證
四川極速動(dòng)力超微粉體設(shè)備制造有限公司
已認(rèn)證
石墨電極的原料及制造工藝
一、石墨電極的原料
1、石墨電極
是采用石油焦、針狀焦為骨料,煤瀝青為粘結(jié)劑,經(jīng)過(guò)混捏、成型、焙燒、浸漬、石墨化、機(jī)械加工等一 系列工藝過(guò)程生產(chǎn)出來(lái)的一種耐高溫石墨質(zhì)導(dǎo)電材料。石墨電極是電爐煉鋼的重要高溫導(dǎo)電材料,通過(guò)石墨電極向電爐輸入電能,利用電極端部和爐料之間引發(fā)電弧產(chǎn)生的高溫作為熱源,使?fàn)t料熔化進(jìn)行煉鋼。其他一些冶煉黃磷、工業(yè)硅、磨料等材料的礦熱爐也用石墨電極作為導(dǎo)電材料。利用石墨電極優(yōu)良而特殊的物理化學(xué)性能,在其他工業(yè)部門也有廣泛的用途。
2、石墨電極的原料
生產(chǎn)石墨電極的原料有石油焦、針狀焦和煤瀝青
(1)石油焦
石油焦是石油渣油、石油瀝青經(jīng)焦化后得到的可燃固體產(chǎn)物。色黑多孔,主要元素為碳,灰分含量很低,一般在0.5%以下。石油焦屬于易石墨化炭一類,石油焦在化工、冶金等行業(yè)中有廣泛的用途,是生產(chǎn)人造石墨制品及電解鋁用炭素制品的主要原料。
石油焦按熱處理溫度區(qū)分可分為生焦和煅燒焦兩種,前者由延遲焦化所得的石油焦,含有大量的揮發(fā)分,機(jī)械強(qiáng)度低,煅燒焦是生焦經(jīng)煅燒而得。中國(guó)多數(shù)煉油廠只生產(chǎn)生焦,煅燒作業(yè)多在炭素廠內(nèi)進(jìn)行。
石油焦按硫分的高低區(qū)分,可分為高硫焦(含硫1.5%以上)、中硫焦(含硫0.5%-1.5%)、和低硫焦(含硫0.5%以下)三種,石墨電極及其它人造石墨制品生產(chǎn)一般使用低硫焦生產(chǎn)。
(2)針狀焦
針狀焦是外觀具有明顯纖維狀紋理、熱膨脹系數(shù)特別低和很容易石墨化的一種優(yōu)質(zhì)焦炭,焦塊破裂時(shí)能按紋理分裂成細(xì)長(zhǎng)條狀顆粒(長(zhǎng)寬比一般在1.75以上),在偏光顯微鏡下可觀察到各向異性 的纖維狀結(jié)構(gòu),因而稱之為針狀焦。
針狀焦物理機(jī)械性質(zhì)的各向異性十分明顯, 平行于顆粒長(zhǎng)軸方向具有良好的導(dǎo)電導(dǎo)熱性能,熱膨脹系數(shù)較低,在擠壓成型時(shí),大部分顆粒的長(zhǎng)軸按擠出方向排列。因此,針狀焦是制造高功率或超高功率石墨電極的關(guān)鍵原料,制成的石墨電極電阻率較低,熱膨脹系數(shù)小,抗熱震性能好。
針狀焦分為以石油渣油為原料生產(chǎn)的油系針狀焦和以精制煤瀝青原料生產(chǎn)的煤系針狀焦。
(3)煤瀝青
煤瀝青是煤焦油深加工的主要產(chǎn)品之一。為多種碳?xì)浠衔锏幕旌衔?,常溫下為黑色高粘度半固體或固體,無(wú)固定的熔點(diǎn),受熱后軟化,繼而熔化,密度為1.25-1.35g/cm3。按其軟化點(diǎn)高低分為低溫、中溫和高溫瀝青三種。中溫瀝青產(chǎn)率為煤焦油的54-56%。煤瀝青的組成極為復(fù)雜,與煤焦油的性質(zhì)及雜原子的含量有關(guān),又受煉焦工藝制度和煤焦油加工條件的影響。表征煤瀝青特性的指標(biāo)很多,如瀝青軟化點(diǎn)、甲苯不溶物(TI)、喹啉不溶物(QI)、結(jié)焦值和煤瀝青流變性等。
煤瀝青在炭素工業(yè)中作為粘結(jié)劑和浸漬劑使用,其性能對(duì)炭素制品生產(chǎn)工藝和產(chǎn)品質(zhì)量影響極大。粘結(jié)劑瀝青一般使用軟化點(diǎn)適中、結(jié)焦值高、β樹(shù)脂高的中溫或中溫改質(zhì)瀝青,浸漬劑要使用軟化點(diǎn)較低、 QI低、流變性能好的中溫瀝青。
二、石墨電極的制造工藝
1、煅燒
炭質(zhì)原料在高溫下進(jìn)行熱處理,排出所含的水分和揮發(fā)份,并相應(yīng)提高原料理化性能的生產(chǎn)工序稱為煅燒。一般炭質(zhì)原料采用燃?xì)饧白陨頁(yè)]發(fā)份作為熱源進(jìn)行煅燒,最高溫度為1250- 1350℃。
(1)煅燒使炭質(zhì)原料的組織結(jié)構(gòu)和物理化學(xué)性能發(fā)生深刻變化,主要體現(xiàn)在提高了焦炭的密度、機(jī)械強(qiáng)度和導(dǎo)電性,提高了焦炭的化學(xué)穩(wěn)定性和抗氧化性能,為后序工序奠定了基礎(chǔ)。
(2)煅燒的設(shè)備主要有罐式煅燒爐、回轉(zhuǎn)窯和電煅燒爐。煅燒質(zhì)量控制指標(biāo)是石油焦真密度不小于2.07g/cm3,電阻率不大于550μΩ.m,針狀焦真密度不小于2.12g/cm3,電阻率不大于500μΩ.m。
(3)原料的破碎處理和配料
①在配料之前,須對(duì)大塊煅后石油焦和針狀焦進(jìn)行中碎、磨粉、篩分處理。
中碎通常是將50mm左右的物料通過(guò)顎式破碎機(jī)、錘式破碎機(jī)、對(duì)輥破碎機(jī)等破碎設(shè)備進(jìn)一步破碎到配料所需的0.5-20mm的粒度料。
②磨粉是通過(guò)懸棍式環(huán)輥磨粉機(jī)(雷蒙磨)、球磨機(jī)等設(shè)備將炭質(zhì)原料磨細(xì)到0.15mm或0.075mm粒徑以下的粉末狀小顆粒的過(guò)程。
③篩分是通過(guò)具有均勻開(kāi)孔的一系列篩子,將破碎后尺寸范圍較寬的物料分成尺寸范圍較窄的幾種顆粒粒級(jí)的過(guò)程,現(xiàn)行電極生產(chǎn)通常需要4-5個(gè)顆粒料粒級(jí)和1-2個(gè)粉料粒級(jí)。
④配料是按配方要求,對(duì)各種粒度的骨料和粉料、粘 結(jié)劑分別計(jì)算、稱量和聚焦的生產(chǎn)過(guò)程。 配方的科學(xué)性適宜性和配料操作的穩(wěn)定性是影響產(chǎn)品質(zhì)量指標(biāo)和使用性能的最重要因素之一。
(4)配方需確定5方面內(nèi)容:
①選擇原料的種類; ②確定不同種類原料的比例; ③確定固體原料粒度組成; ④確定粘結(jié)劑的用量;⑤確定添加劑的種類和用量。
(6)返回料的回用(生碎、石墨碎、焙燒碎)
(7)配方基本原則:球體最緊密堆積原理
(8)電極配方中最大顆粒尺寸的確定
大顆粒配方
混捏
在一定溫度下將定量的各種粒度炭質(zhì)顆粒料和粉料與定量的粘結(jié)劑攪拌混合均勻,捏合成可塑性糊料的工藝過(guò)程稱為混捏。
(1)混捏的過(guò)程:干混(20-35 min)濕混(40-55 min)
(2)混捏的作用:
①干混時(shí)使各種原料混合均勻,同時(shí)使不同粒度大小的固體炭質(zhì)物料均勻地混合和填充,提高混合料的密實(shí)度;
②加入煤瀝青后使干料和瀝青混合均勻,液態(tài)瀝青均勻涂布和浸潤(rùn)顆粒表面,形成一層瀝青粘結(jié)層,把所有物料互相粘結(jié)在一起,進(jìn)而形成均質(zhì)的可塑性糊料,有利于成型;
③部分煤瀝青浸透到炭質(zhì)物料內(nèi)部空隙,進(jìn)一步提高了糊料的密度和粘結(jié)性。
3、成型
炭材料的成型是指混捏好的炭質(zhì)糊料在成型設(shè)備施加的外部作用力下產(chǎn)生塑性變形,最終形成具有一定形狀、尺寸、密度和強(qiáng)度的生坯(或稱生制品)的工藝過(guò)程。
成型的種類、設(shè)備及所生產(chǎn)產(chǎn)品:
成型方法 | 常用設(shè)備 | 主要產(chǎn)品 |
模壓 | 立式液壓機(jī) | 電碳、低檔次細(xì)結(jié)構(gòu)石墨 |
擠壓 | 臥式液壓擠壓機(jī) 螺桿擠壓機(jī) | 石墨電極、方電極 |
振動(dòng)成型 | 振動(dòng)成型機(jī) | 鋁用碳磚、高爐碳磚 |
等靜壓 | 等靜壓成型機(jī) | 各向同性石墨、異性石墨 |
4、擠壓的操作
(1)涼料:圓盤涼料、圓筒涼料、混捏式?jīng)隽系确绞?/span>
排出揮發(fā)份、降低至適宜溫度(90-120℃)增加粘結(jié)力,使糊料塊度均勻利于成型
20-30 min
(2)裝料:壓機(jī)升擋板----分2-3次下料----4-10MPa壓實(shí)
(3)預(yù)壓:壓力20-25MPa,時(shí)間3-5min,同時(shí)抽真空
(4)擠壓:壓機(jī)降擋板----5-15MPa擠壓----剪切----翻入冷卻 水槽
(5)擠壓的技術(shù)參數(shù):壓縮比、壓機(jī)料室及嘴型溫度、涼料溫度、預(yù)壓壓力時(shí)間、擠壓壓力、擠壓速度、冷卻水溫度
(6)生坯的檢查:體積密度、外觀敲擊、剖析
5、焙燒
是炭制品生坯在填充料保護(hù)下、裝入專門設(shè)計(jì)的加熱爐內(nèi)進(jìn)行高溫?zé)崽幚?/span>, 使生坯中的煤瀝青炭化的工藝過(guò)程。煤瀝青炭化后形成的瀝青焦將炭質(zhì)骨料和粉料顆粒固結(jié)在一起, 焙燒后的炭制品具有較高的機(jī)械強(qiáng)度、較低的電阻率、較好的熱穩(wěn)定性和化學(xué)穩(wěn)定性。
(1)焙燒是炭素制品生產(chǎn)的主要工序之一, 也是石墨電極生產(chǎn)三大熱處理過(guò)程中的重要一環(huán), 焙燒生產(chǎn)周期較長(zhǎng)(一焙22-30天,二焙依爐型5-20天), 而且能耗較高。生坯焙燒的質(zhì)量對(duì)成品質(zhì)量和生產(chǎn)成本都有一定影響。
(2)生坯內(nèi)煤瀝青在焙燒過(guò)程中焦化,排出10%左右的揮發(fā)份,同時(shí)體積產(chǎn)生2-3%的收縮,質(zhì)量損失8-10%。炭坯的理化性能也發(fā)生了顯著變化,由于氣孔率增加體積密度由1.70g/cm3降為1.60g/cm3,電阻率10000μΩ.m左右降至40-50μΩ.m,焙燒坯的機(jī)械強(qiáng)度也大為提高。
(3)二次焙燒是焙燒品浸漬后進(jìn)行再次焙燒,使浸入焙燒品孔隙中的瀝青炭化的工藝過(guò)程。生產(chǎn)體積密度要求較高的電極(除RP以外的所有品種)和接頭坯料需進(jìn)行二焙,接頭坯料還需進(jìn)行三浸四焙或二浸三焙。
(4)焙燒爐主要爐型:
①連續(xù)作業(yè)----環(huán)式爐(帶蓋、不帶蓋)、隧道窯
②間歇作業(yè)----倒焰窯、車底式焙燒爐、箱式焙燒爐
(5)焙燒曲線及最高溫度:
一次焙燒----320、360、422、480小時(shí),1250 ℃
二次焙燒----125、240 、280 小時(shí),700-800 ℃
(6)焙燒品的檢查:外觀敲擊、電阻率、體積密度、抗壓強(qiáng)度、內(nèi)部結(jié)構(gòu)剖析
浸漬是將炭材料置于壓力容器中,在一定的溫度和壓力條件下將液態(tài)浸漬劑瀝青浸入滲透到制品電極孔隙中的工藝過(guò)程。目的是降低制品氣孔率,增加制品體積密度和機(jī)械強(qiáng)度,改善制品的導(dǎo)電和導(dǎo)熱性能。
浸漬的工藝流程及相關(guān)技術(shù)參數(shù)是:焙燒坯——表面清理——預(yù)熱(260-380 ℃,6-10小時(shí))——裝入浸漬罐——抽真空(8-9KPa,40-50min)——注瀝青(180-200 ℃)——加壓(1.2-1.5MPa,3-4小時(shí))——返瀝青——冷卻(罐內(nèi)或罐外)
(7)浸漬品的檢查:浸漬增重率G=(W2-W1)/W1×100%
一次浸漬品增重率≥14%
二次浸漬品增重率≥9%
三次浸漬品增重率≥5%
6、石墨化
是指在高溫電爐內(nèi)保護(hù)介質(zhì)中把炭制品加熱到2300 ℃以上,使無(wú)定形亂層結(jié)構(gòu)炭轉(zhuǎn)化成三維有序石墨晶質(zhì)結(jié)構(gòu)的高溫?zé)崽幚磉^(guò)程。平面六角網(wǎng)格層狀結(jié)構(gòu)
(1)石墨化的目的和作用:
①提高炭材料的導(dǎo)電、導(dǎo)熱性(電阻率降低4-5倍,導(dǎo)熱性提高約10倍);
②提高炭材料的抗熱振性能和化學(xué)穩(wěn)定性(線膨脹系數(shù)降低50-80%);
③使炭材料具有潤(rùn)滑性和抗磨性;
④排出雜質(zhì),提高炭材料的純度(制品的灰分由0.5-0.8%降到0.3%左右)。
(2)石墨化過(guò)程的實(shí)現(xiàn):
炭材料的石墨化是在2300-3000 ℃高溫下進(jìn)行的,故工業(yè)上只有通過(guò)電加熱方式才能實(shí)現(xiàn),即電流直接通過(guò)被加熱的焙燒品,這時(shí)裝入爐內(nèi)的焙燒品既是通過(guò)電流產(chǎn)生高溫的導(dǎo)體,又是被加熱到高溫的對(duì)象。
目前廣泛采用的爐型有艾奇遜(Acheson)石墨化爐和內(nèi)熱串接(LWG)爐。前者產(chǎn)量大、溫差大、電耗較高,后者加熱時(shí)間短、電耗低、電阻率均勻但不好裝接頭。
石墨化工藝過(guò)程的控制是通過(guò)測(cè)溫確定與升溫情況相適應(yīng)的電功率曲線進(jìn)行控制,通電時(shí)間艾奇遜爐50-80小時(shí),LWG爐9-15小時(shí)。
石墨化的電耗很大,一般為3200-4800KWh,工序成本約占整個(gè)生產(chǎn)成本的20-35%
(3)石墨化品的檢查:外觀敲擊、電阻率測(cè)試
7、機(jī)械加工
炭石墨材料機(jī)械加工的目的是依靠切削加工來(lái)到達(dá)所需要的尺寸、形狀、精度等,制成符合使用要求電極本體和接頭。
石墨電極加工分為電極本體和接頭兩個(gè)獨(dú)立加工過(guò)程。
①本體加工包括鏜孔與粗平端面、車外圓與精平端面和銑螺紋3道工序,圓錐形接頭的加工可分為6道工序:切斷、平端面、車錐面、銑螺紋、鉆孔安栓和開(kāi)槽。
②電極接頭連接方式:圓錐形接頭連接(一吋三扣和一吋四扣)、圓柱形接頭連接、凹凸連接(公母扣連接)
(2)加工精度的控制:螺紋錐度偏差、螺紋螺距、接頭(孔)大徑偏差、接頭孔同軸度、接頭孔垂直度、電極端面平整度、接頭四點(diǎn)偏差等。用專用環(huán)規(guī)和板規(guī)等檢查。
(3)成品電極的檢查:精度、重量、長(zhǎng)度、直徑、體積密度、電阻率、預(yù)裝配合精度等。
三、石墨電極的質(zhì)量指標(biāo)
2290655731下表為方大炭素的RP、HP及UHP電極內(nèi)控質(zhì)量標(biāo)準(zhǔn)
規(guī)格 | 普通功率 | 高功率 | 超高功率 | ||||
≤φ300 | ≥φ350 | ≤φ400 | ≥φ450 | ≤φ400 | ≥φ450 | ||
電阻率 μΩ·m不大于 | 電極 | 8.5 | 6.5 | 5.5 | |||
接頭 | 6.5 | 5.5 | 4.5 | ||||
體積密度g/cm3 不小于 | 電極 | 1.53 | 1.52 | 1.62 | 1.62 | 1.67 | 1.66 |
接頭 | 1.69 | 1.73 | 1.75 | ||||
抗折強(qiáng)度Mpa 不小于 | 電極 | 8.5 | 7.0 | 10.5 | 9.8 | 11.0 | |
接頭 | 15.0 | 16.0 | 20.0 | ||||
彈性摸量Gpa 不大于 | 電極 | 9.3 | 12.0 | 14.0 | |||
接頭 | 14.0 | 16.0 | 18.0 | ||||
熱膨脹系數(shù) 10-61/℃不大于 | 電極 | 2.9 | 2.4 | 1.5 | |||
接頭 | 2.8 | 2.2 | 1.4 |
體積密度是石墨電極試樣的質(zhì)量與其體積的比值,單位g/cm3,體積密度越大說(shuō)明電極越密實(shí),與強(qiáng)度、抗氧化性能是正相關(guān),一般而言,同品種電極體積密度越大,其電阻率也越低。
提高體積密度的途徑是:調(diào)整配方、增加小粒級(jí)料和粉料用量,用真密度高的焦,使用結(jié)焦值高的瀝青和增加浸漬次數(shù)等。
電阻率是來(lái)衡量電極的導(dǎo)電能力的參數(shù),是指電流通過(guò)導(dǎo)體時(shí),導(dǎo)體對(duì)電流阻力的一種性質(zhì),數(shù)值上等于長(zhǎng)度為1m、截面積為1m2的導(dǎo)體在一定溫度條件下的電阻值,單位μΩ·m。電阻率越低,電極在使用中導(dǎo)電性越好、消耗就越低。
降低電阻率的途徑有:使用優(yōu)質(zhì)原料,提高制品體積密度,提高石墨化溫度等。
抗折強(qiáng)度是表征石墨材料的力學(xué)性能的參數(shù),也叫抗彎強(qiáng)度,是指當(dāng)外力與物體軸線相垂直,物體受外力作用后先呈彎曲到折斷瞬間的極限抵抗能力,單位為MPa。石墨材料的強(qiáng)度有個(gè)與其他金屬非金屬顯著不同的特點(diǎn),其強(qiáng)度隨溫度升高而增大,在2000-2500 ℃達(dá)到最高,為常溫的1.8-2倍,之后有所下降。強(qiáng)度高的電極、接頭,在使用中越不易折斷。
提高抗折強(qiáng)度的途徑是:減小配方中焦炭的粒度,提高炭質(zhì)原料強(qiáng)度,提高制品的體積密度,減少制品內(nèi)部缺陷等。
彈性模量是力學(xué)性能的一個(gè)重要方面,是衡量材料彈性形變能力的指標(biāo),指材料在彈性變形范圍內(nèi),應(yīng)力和應(yīng)變的比值,單位為GPa。彈性模量越大,要產(chǎn)生一定彈性變形所需的應(yīng)力越大,簡(jiǎn)單講,彈性模量越大材料越脆,彈性模量越小材料越柔。
彈性模量的高低對(duì)電極使用起一個(gè)綜合性的作用,制品的體積密度越高越密實(shí),彈性模量越大,但制品的抗熱振性能越差,越易產(chǎn)生開(kāi)裂掉塊。在生產(chǎn)中,往往通過(guò)配方粒級(jí)的調(diào)整、制品體積密度的高低掌握一個(gè)比較適應(yīng)使用要求的彈性模量值。
熱膨脹系數(shù)是指材料受熱后膨脹程度的度量,即當(dāng)溫度升高1℃時(shí),引起單位的固體材料試樣在某一特定方向上的膨脹比例常數(shù),稱為沿該方向的線膨脹系數(shù),單位1×10-6/℃。在沒(méi)有特別注明之處,熱膨脹系數(shù)均指線膨脹系數(shù),石墨電極軸向和徑向線膨脹系數(shù)差異很大,徑向要比軸向大0.8-1倍,石墨電極質(zhì)量指標(biāo)中的熱膨脹系數(shù)是指軸向熱膨脹系數(shù)。
石墨電極的熱膨脹系數(shù)是非常重要的熱學(xué)參數(shù),數(shù)值越低,表明制品的熱穩(wěn)定性越強(qiáng),抗氧化性越高,表現(xiàn)在使用上反映出折斷越少,消耗越低。
降低熱膨脹系數(shù)的途徑:主要由原料固有性能決定使用質(zhì)量好的原料,配方使用粒度較大配方或增加大顆粒用量(但會(huì)使制品密度和強(qiáng)度降低)。
灰分是指制品中除碳石墨之外的其他固體元素含量。石墨電極中的灰分主要受所用原料的灰分大小影響,石油焦針狀焦灰分較低,所以石墨電極灰分一般不超過(guò)0.5%,灰分含量在1%以內(nèi)對(duì)煉鋼無(wú)明顯影響,但灰分中的雜質(zhì)元素會(huì)降低電極的抗氧化性能。
抗熱振因子是表征抗熱振性能的參數(shù),抗熱振性能是材料自身的一種特性,它表述的是承受急冷急熱的一種性能,換句話說(shuō),是材料在一定的溫度梯度之下抗碎裂的一種性能 ,是影響電極使用的一個(gè)很重要的綜合性的因素。
K——抗熱震因子,w/m;σ——抗拉強(qiáng)度,MPa;E——彈性模量,MPa;λ——熱導(dǎo)率,w/m·k;α——熱膨脹系數(shù),1/K
K為一相對(duì)值,該值越大,抗熱振性能就越強(qiáng)。
石墨電極的K值與其在電弧爐中的表現(xiàn)有著較高的相關(guān)性,即較高的K值,對(duì)應(yīng)于電極較低的破碎和斷裂。
四、電爐煉鋼簡(jiǎn)介及石墨電極的消耗機(jī)理
1、電爐煉鋼簡(jiǎn)介
近現(xiàn)代煉鋼方法主要有轉(zhuǎn)爐煉鋼法、平爐煉鋼法和電爐煉鋼法。平爐煉鋼法已基本被淘汰,電爐煉鋼法與轉(zhuǎn)爐煉鋼法最根本的差別在于,電爐煉鋼法是以電能作為熱源,而電弧爐煉鋼是應(yīng)用得最為普遍的電爐煉鋼方法。我們通常所說(shuō)的電爐煉鋼,主要是指電弧爐煉鋼,因?yàn)槠渌愋偷碾姞t如感應(yīng)電爐、電渣爐等所煉的鋼數(shù)量較少。
電弧爐煉鋼是靠電極和爐料間放電產(chǎn)生的電弧,使電能在弧光中轉(zhuǎn)變?yōu)闊崮埽⒔柚椛浜碗娀〉闹苯幼饔眉訜岵⑷刍饘俸蜖t渣,冶煉出各種成分的鋼和合金的一種煉鋼方法。
電爐煉鋼的特點(diǎn)
電爐煉鋼與其他煉鋼方法相比較,有其獨(dú)特的優(yōu)點(diǎn)。電弧爐煉鋼是靠電弧進(jìn)行加熱的,其溫度可以高達(dá)2000℃以上,超過(guò)了其他煉鋼爐用一般燃料燃燒加熱時(shí)所能達(dá)到的最高溫度。同時(shí),熔化爐料時(shí)熱量大部分是在被加熱的爐料包圍中產(chǎn)生的,而且無(wú)大量高溫廢氣帶走的熱損失,所以熱效率比平爐、轉(zhuǎn)爐煉鋼法要高。用電能加熱還能精確控制溫度。因?yàn)闋t內(nèi)沒(méi)有可燃燒氣體,所以可以根據(jù)工藝要求在各種不同的氣氛中進(jìn)行加熱,也可在任何壓力或真空中進(jìn)行加熱。由于電弧爐煉鋼具有上述特點(diǎn),能保證冶煉含磷、硫、氧低的優(yōu)質(zhì)鋼,能使用各種元素(包括鋁、鐵等容易被氧化的元素)來(lái)使鋼合金化,冶煉出各種類型的優(yōu)質(zhì)鋼和合金鋼。
電爐煉鋼另一個(gè)優(yōu)點(diǎn)是基建投資少,占地面積小,流程斷,效率高。尤其是和轉(zhuǎn)爐相比,它可以用廢鋼作為原料,不像轉(zhuǎn)爐那樣需要熱鐵水,所以不需要一套龐大的煉鐵和煉焦系統(tǒng)。
從長(zhǎng)遠(yuǎn)觀點(diǎn)看,電能的成本穩(wěn)定,供應(yīng)方便;電孤?tīng)t設(shè)備簡(jiǎn)單,操作方便;還比較易于控制污染。由此可見(jiàn),用電弧爐煉鋼的優(yōu)越性是相當(dāng)大的,所以現(xiàn)在世界各國(guó)都在大力發(fā)展純氧頂吹轉(zhuǎn)爐的同時(shí),穩(wěn)步地發(fā)展電弧爐煉鋼技術(shù)。當(dāng)前電弧爐的發(fā)展趨勢(shì)是:發(fā)展大型電弧爐;發(fā)展超高功率供電技術(shù);采用各種爐外精煉法;發(fā)展直接還原法煉鋼,逐步擴(kuò)大機(jī)械化自動(dòng)化及用電子計(jì)算機(jī)進(jìn)行過(guò)程控制等。
目前世界范圍電爐鋼占粗鋼比例為35%左右,我國(guó)只有15-16%,還有很大發(fā)展空間。
電爐的分類
①按爐襯耐火材料性質(zhì):酸性電爐、堿性電爐
②按電流特性:交流和直流電爐
③按功率大小:普通功率、高功率和超高功率電爐
④按廢鋼預(yù)熱方式:豎爐、雙殼爐、爐料連續(xù)預(yù)熱電爐
⑤按出鋼方式:槽式出鋼、偏心底出鋼(EBT)、中心底出鋼(CBT)及水平出鋼(HOT)電爐等
電爐煉鋼的流程
補(bǔ)爐→裝料(1-3次)→熔化期(起弧、穿井、主熔、升溫四個(gè)階段)→氧化期(脫磷、脫碳、去氣)→還原期(脫硫、脫氧、調(diào)成分)→出鋼澆鑄或爐外二次精煉。
五、石墨電極的消耗機(jī)理
石墨電極在電爐煉鋼中的消耗量主要與電極本身質(zhì)量有關(guān),也與煉鋼的爐況(如爐子新舊、有無(wú)機(jī)械故障、是否連續(xù)生產(chǎn)等)和煉鋼操作(如冶煉鋼種、吹氧時(shí)間、爐料情況等)關(guān)系很大。這里只探討石墨電極本身的消耗情況,其消耗機(jī)理有以下幾方面:
端部消耗
包括電弧高溫引起的石墨材料升華以及電極端部與鋼水及爐渣發(fā)生化學(xué)反應(yīng)的損失。端部高溫升華速率主要取決于通過(guò)電極的電流密度,其次與電極側(cè)部氧化后的直徑大小有關(guān),端部消耗還與是否用電極插入鋼水增炭有關(guān)。
側(cè)部氧化
電極的化學(xué)成分是碳,碳在一定條件下與空氣、水蒸氣、二氧化碳都會(huì)發(fā)生氧化反應(yīng),電極側(cè)部氧化量與單位氧化速率和暴露面積有關(guān)。一般情況下,電極側(cè)部氧化量要占電極總消耗量的50%左右。近年來(lái)為了提高電爐冶煉速度,更增加了吹氧操作的頻次,導(dǎo)致電極的氧化損失增加。在煉鋼過(guò)程中經(jīng)常觀察電極軀干的發(fā)紅程度和下端的錐度是衡量電極抗氧化能力的直觀方法。
殘端損失
電極連續(xù)使用到上下兩根電極連接處時(shí),一小段電極或接頭(即殘?bào)w)因本體的氧化變細(xì)或裂紋的貫通而產(chǎn)生脫離。殘端損失的大小與接頭形狀扣型、電極內(nèi)部結(jié)構(gòu)、電極柱的振動(dòng)、撞擊有關(guān)。
表面剝落及掉塊
在冶煉過(guò)程中急冷急熱,電極自身的抗熱振性能差導(dǎo)致的結(jié)果。
電極折斷
包括電極軀干折斷和接頭折斷。電極折斷與石墨電極和接頭的自身質(zhì)量、加工配合有關(guān),也與煉鋼操作有關(guān),產(chǎn)生原因往往是鋼廠與電極生產(chǎn)廠爭(zhēng)議的焦點(diǎn)。
相關(guān)產(chǎn)品
更多
相關(guān)文章
更多
技術(shù)文章
2019-12-05技術(shù)文章
2019-06-02技術(shù)文章
2019-05-02技術(shù)文章
2018-12-26