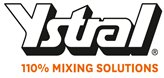
德國ystral公司
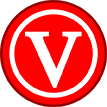
已認(rèn)證
德國ystral公司
已認(rèn)證
Ystral Conti-TDS - A new Dispersion Technology in Lacquer and Paint Production Dr. Hans-Joachim Jacob | 用于涂料生產(chǎn)的一種新型分散技術(shù) — 德國ystral公司的Conti-TDS Dr. Hans-Joachim Jacob |
Dissolvers were invented in the middle of the last century and have survived in lacquer and paint production until today. They have too many disadvantages, limitations and negative effects on the final product. | 高速分散機(jī)發(fā)明于上世紀(jì)中葉且仍在當(dāng)今涂料的生產(chǎn)上使用。此類設(shè)備存在太多缺點(diǎn)和制約,對成品產(chǎn)生負(fù)面影響。 |
The ystral Conti-TDS - a new and advanced dispersion technology - has started to displace traditional High Speed Dissolvers in Lacquer and Paint Production. This new technology enables enormous reductions in production costs and process times. Additional effects are a higher degree of dispersion, improved quality and raw material savings. The energy consumption is reduced to about 30% compared to the old dissolver technology. | 德國ystral公司的Conti-TDS 是一種新型的、先進(jìn)的分散技術(shù),已開始在涂料生產(chǎn)上替代傳統(tǒng)的高速分散機(jī)。這項(xiàng)新技術(shù)能夠極大的降低生產(chǎn)成本和減少加工時(shí)間,達(dá)到更高水平的分散度,改善產(chǎn)品品質(zhì)和節(jié)約原料等的附加效果。相比之下,這項(xiàng)新技術(shù)的能耗降低至只有傳統(tǒng)高速分散機(jī)的30%左右。 |
Ystral Conti-TDS | 德國ystral Conti-TDS 這項(xiàng)新技術(shù)靈活性高并且可以根據(jù)需要容易的擴(kuò)展。與同樣產(chǎn)能的傳統(tǒng)高速分散機(jī)相比,投資成本要低40%以上。 |
Dispersion is the most important process in lacquer and paint production and has the highest influence on the quality of the final product. The better the dispersion the higher is the efficiency of the dispersed pigments, extenders, rheology modifiers and all other functional additives in the final coating. Traditional high speed dissolvers are simple free rotating discs with up- and down-bent teeth at their circumference. Due to the wide distance between the rotating dissolver disc and the static wall of the vessel the shear gradient is very low: just about 50 reciprocal seconds. To create shear forces with such a low shear rate a dissolver needs a very high viscous liquid or at least a shear thickening or dilatant rheology. Lacquers and paints have exactly the opposite rheology: they are low viscous, shear thinning and thixotropic. A dissolver cannot create significant shear in a low viscous lacquer or paint. To shear with a dissolver the viscosity has to be increased extremely. For that reason the dissolver process starts with more thickeners than required and just a part of the liquids to get a higher viscosity. This is completely paradox since the most ingredients which have to be dispersed are very fine powders (pigments, silica, fillers and extenders). Making a liquid extra high viscous before adding finest powders is absurd. The higher the viscosity the worse is the wetting and dispersion of fine powders. A high viscous liquid will not get into smallest capillaries and cannot wet fine particles as fast and complete as a low viscous liquid. The consequences are stable agglomerates, low qualities, extra-long dispersing and milling times, heat generation and a waste of energy. Adding thickeners at begin of the process is negative for another reason: Most thickeners are shear-sensitive polymers. During dispersion the polymers get partially destroyed. Their effect goes down in an uncontrolled manner. For that reason you have to add more thickeners than required and you get uncontrolled and unpredictable viscosity levels at the end of the dissolver process. Finally you have to adjust the viscosity again. In other industries dissolvers have disappeared since years. Now the dispersion technology in lacquer and paint production has started to change to Conti-TDS – worldwide.
| 分散是涂料生產(chǎn)中最重要的工序,其對成品品質(zhì)的影響最大。分散的效果越好,最終涂層中分散的顏料、填充劑、流變改性劑和所有其他功能添加劑的效率就越高。 傳統(tǒng)的高速分散機(jī)是簡單的自由旋轉(zhuǎn)的圓盤片,其圓周上有向上和向下彎曲的齒。由于轉(zhuǎn)動(dòng)的分散盤與容器的靜態(tài)壁之間的距離較寬,剪切速率非常低:大約只有50S-1 。在如此低的剪切速率下產(chǎn)生的剪切力,高速分散機(jī)需要很高粘度的液體或至少產(chǎn)品具有剪切增厚或膨脹的流變特性,然而涂料具有與之截然相反的流變性:它們是低粘度的、具有剪切變稀和觸變性。高速分散機(jī)無法在低粘性油漆或涂料中產(chǎn)生顯著的剪切效應(yīng)。利用高速分散機(jī)進(jìn)行剪切分散,必須極大提高產(chǎn)品的粘度。因此,高速分散機(jī)的分散過程從一開始就需要加入比需要的更多的增稠劑,且僅加入部分液體以獲得更高的粘度。 這實(shí)際上是完全矛盾的,因?yàn)楸仨毐环稚⒌拇蠖鄶?shù)的添加成分都是些非常精細(xì)的粉料 (顏料、硅土、填料和填充劑),在添加微細(xì)的粉料之前先將液體制備成高粘度是很荒謬的。粘度越高,對微細(xì)粉料的潤濕與分散就越差。高粘度的液體無法進(jìn)入最小的毛細(xì)管,無法像低粘性液體一樣快速和完全的潤濕顆粒。其后果導(dǎo)致穩(wěn)定的團(tuán)塊,品質(zhì)低,分散和研磨時(shí)間加長,產(chǎn)生熱量并且浪費(fèi)能量。 在分散開始時(shí)添加增稠劑有負(fù)面作用的另一個(gè)原因:大多數(shù)的增稠劑是剪切敏感的聚合物,在分散過程中,聚合物會(huì)有一部分受到破壞,它們的功效以不可控的方式下降。因此,增稠劑的添加必須比必要的更多,當(dāng)高速分散結(jié)束時(shí),得到的是無控制的和不可預(yù)測的粘度。最后,粘度必須再調(diào)整。 在其它行業(yè),高速分散機(jī)已消失多年。如今油漆和涂料生產(chǎn)的分散技術(shù)已開始在全球范圍內(nèi)向Conti-TDS轉(zhuǎn)變。 |
Conti-TDS Technology | Conti-TDS技術(shù) |
Ystral Conti-TDS Technology is based on an inline dispersing machine which is able to induct and disperse powders into liquids under high speed and vacuum. The machine is installed outside the process tank and recirculates the liquid with high speed. Additional pumps are not required.
德國ystral公司Conti-TDS 技術(shù)是基于一種在線分散機(jī),能夠在高速運(yùn)轉(zhuǎn)和真空下導(dǎo)入粉體,使粉體分散至液體中。該機(jī)器安裝在工藝混合罐外部,讓液體以高速打循環(huán),無需額外的泵。
Picture 1: ystral-Conti-TDS with process tank and big-bag station
圖 1:ystral-Conti-TDS 連接循環(huán)罐和大袋解包站
The core of the machine is the dispersing chamber equipped with high shear tools. In the high-shear dispersing zone it creates a shear rate of 50.000 reciprocal seconds. This is 1000 times higher shear compared to the dissolver. High liquid viscosities or additional thickeners are not required. Exactly in this zone the machine creates a very strong vacuum. With this vacuum it inducts powder directly from bags, bag tipping stations, hoppers, drums, containers and big bags into the liquid. No vacuum tank and no vacuum pump is required which pulls uncontrolled amounts of powder or effluent vapor out of the liquid into filters or exhaust systems as it happens in vacuum dissolvers. The induction is dust-free because 100% of all the powder goes into the liquid. Dust pollution of the working area is completely avoided. The powder is inducted into the recirculating liquid loop and arrives in the vessel as a liquid dispersion. No dust appears above the liquid; no partially wetted agglomerates and crusts are built up above the liquid surface and then fall into the liquid and reduce product quality, a common problem with dissolvers. | 機(jī)器的核心是內(nèi)部裝配有高剪切部件的分散腔。在該高剪切分散區(qū)能產(chǎn)生50’000S-1的剪切速率。這個(gè)剪切速率比高速分散機(jī)高1’000倍,不需要提高液體粘度或額外添加更多的增稠劑。 在此分散腔內(nèi)機(jī)器能產(chǎn)生一個(gè)很強(qiáng)的真空,利用這個(gè)真空,機(jī)器可以直接從袋子、包袋的傾倒站、粉料斗、各種桶、容器和大袋中吸入粉體,使粉料進(jìn)入液體。不需要將混合罐抽真空,也不需要加真空泵,帶抽真空的高速分散機(jī)會(huì)帶走無法控制的粉體量或使液體中產(chǎn)生的廢蒸汽進(jìn)入過濾器或排氣系統(tǒng)。粉體吸入是無塵的,因?yàn)?/span>100%的所有粉料都會(huì)被導(dǎo)入液體中,從而杜絕了工作區(qū)域的粉塵污染。 粉末被吸入液體的循環(huán)回路,成為液狀分散體到達(dá)容器。不再有粉塵出現(xiàn)在液體之上; 不再出現(xiàn)局部浸濕的團(tuán)聚體和結(jié)殼積聚在液體表面后又落入液體中和品質(zhì)降低這些高速分散機(jī)的常見問題。 |
Picture 2: ystral Conti-TDS with liquid and powder connections
圖2:ystral conti-TDS 與液體和粉體連接
The dispersion of the powder into the liquid is always done under equal, constant and controlled conditions, independent from the speed of the operator. The product quality is absolutely reproducible, even for different batch sizes.
將粉料分散至液體中始終是在相同的、連續(xù)的并且是受控的條件下完成的,與操作人員的動(dòng)作快慢無關(guān)。產(chǎn)品質(zhì)量可完全重復(fù)再現(xiàn),即便對于不同大小的批量。
Constant quality has been one of the biggest problems with dissolvers. Particle size, color strength, viscosity, matting effect and film formation are influenced by the way how the operator has added the powder. The quality changed from batch to batch, from operator to operator. Slower powder addition caused longer process times, higher temperatures, lower viscosities. Faster addition caused more agglomerates and further processing time, longer shear, higher temperatures and lower viscosity. Dissolver batches always had to be quality checked – adjusted – checked and adjusted again. These steps took time and blocked the process tanks during waiting for the QC results. | 達(dá)到恒定的品質(zhì)一直是高速分散機(jī)存在的最大問題之一。顆粒度、色強(qiáng)度、粘度、消光效應(yīng)和成膜效果都受到操作者添加粉料方式的影響。從批量到批量,從操作員到操作員,品質(zhì)都在變化。較慢地添加粉體導(dǎo)致加工時(shí)間過長,溫度更高,粘度更低;較快地添加粉體又會(huì)導(dǎo)致更多的結(jié)塊和進(jìn)一步延長加工處理時(shí)間,更長時(shí)間的剪切,更高的溫度和更低的粘度。高速分散機(jī)的批量總是必須經(jīng)過質(zhì)檢- 調(diào)整- 再質(zhì)檢和再調(diào)整。這些步驟花費(fèi)時(shí)間,等待QC結(jié)果的時(shí)間阻擋了工藝混合罐。 |
Some Results with Conti-TDS The Conti-TDS produces absolutely constant qualities. The viscosity is constant. And thickeners are not destroyed – what means that often up to 20% of the thickener can be taken out. This is the amount which is typically over dosed and destroyed by the long dissolver process. Picture 3 shows a typical particle size distribution for the induction and dispersion of titanium dioxide.
Immediately after induction the result is already much better than reference samples produced with Dissolver and Mill. The medium particle size is already 0.46 μm. 99,9 % of the particles are below 2 μm. Not any oversized particle is visible. The distribution is very narrow. After 120 sec additional dispersion the medium particle size goes down to 0.38 μm. 100 % are below 2μm and 98% are below 1μm.
The color strength of the titanium dioxide dispersions produced with Conti-TDS is always much higher. For that reason the amount of Titanium Dioxide may be reduced with even better performance than dissolver dispersions. Titanium dioxide is the most important pigment in lacquer, paint and ink production. It covers more than 59% of the global pigment demand. The prices for titanium dioxide are rising since 2009. Companies which are using the Conti-TDS for titanium dioxide are reporting about enormous savings. They save time, energy and a significant amount of raw material because of the better dispersion. But even all other pigments, matting agents, extenders and fillers are dispersed faster and with better results – for all water born and solvent born lacquers, paints and printing inks.
Installation and Operation The machine is installed in recirculation with a process tank. This way it operates independently from vessel size and filling level. To double the capacity with minimum additional costs one machine is often installed between two vessels (picture 4). You need just one machine, one control system and one powder addition point to double the production output. |
Conti-TDS的一些結(jié)果 Conti-TDS可以生產(chǎn)出完全均一恒定的質(zhì)量。粘度是恒定的,增稠劑也不會(huì)被破壞,這意味著通常高達(dá)20%的增稠劑可以省去,這個(gè)數(shù)量也是通常被過量添加和被高速分散機(jī)長時(shí)間溶解所破壞的量。
圖3顯示了鈦白粉的吸入和分散的典型粒徑分布 圖 3:鈦白粉被吸入后分散30秒、60秒和120秒的粒徑分布
在粉體被吸入后可即刻獲得比高速分散機(jī)和磨機(jī)生產(chǎn)的參照樣品好得多的結(jié)果。中粒徑已達(dá)到0.46μm。99,9%的粒子小于2μm。沒有任何大的粒子可見,粒徑分布很窄。經(jīng)120秒延時(shí)分散后中粒徑下降至0.38μm,100%小于2μm和98%小于1μm。 使用Conti-TDS 生產(chǎn)的鈦白粉分散體的色強(qiáng)度總是要高很多。因此,與高速分散機(jī)相比,即便減少鈦白粉的用量都能達(dá)到更好的品質(zhì)性能。 鈦白粉是生產(chǎn)油漆、涂料和油墨最重要的顏料。它覆蓋了全球顏料59%以上的需求。鈦白粉的價(jià)格自2009年以來就處于上漲。使用Conti-TDS加工鈦白粉的廠家的報(bào)告了他們巨大的節(jié)省。因?yàn)檫@種更好的分散,他們節(jié)省了時(shí)間、能耗以及大量的原料。 然而所有其它顏料、消光劑、填充劑和填料,都能被分散得更快,達(dá)到更好的效果—對于所有水基和溶劑基的油漆、涂料和印刷油墨。 安裝與運(yùn)行 機(jī)器安裝在與一臺工藝罐的循環(huán)連接的回路中。如此,機(jī)器的運(yùn)行不受罐體大小和罐的料位影響。以最小的花費(fèi)讓產(chǎn)能翻番的辦法經(jīng)常是將一臺機(jī)器安裝在兩臺工藝罐之間(如圖4)。你只需一臺機(jī)器、一個(gè)控制系統(tǒng)及一個(gè)粉料加料口就能讓產(chǎn)能翻番。 |
Picture 4: Conti-TDS-5 between two process tanks
圖4:兩臺工藝儲罐之間的 Conti-TDS-5
During production in one vessel the other vessel is discharged from the last batch and filled with the liquid for the next batch already. In the average 50 seconds after finishing the powder induction the required particle size is reached and the product is ready to transfer. When the batch is ready to discharge the machine automatically switches over to the second tank and starts the process there. This way it is possible to produce up to 20.000 kg finished paint per hour with just one machine, even in a continuous and uninterrupted production.
All Conti-TDS systems have an integrated and paint industry approved automatic cleaning unit. To keep the process system always clean every single batch includes a cleaning step. A part of the process liquid is added through the cleaning heads and keeps the tank and all relevant parts clean. Even if the following batch is the same product the vessel is cleaned automatically. Additional cleaning with extra liquid is possible if there is a product change between incompatible materials or different colours. Inside the process tanks there are high effective jet stream mixers installed which are moving and turning the liquid vertically. These mixers provide an instantaneous homogeneity. This is important because of the high speed powder addition. Simple agitators with mainly horizontal rotation are not able to mix the liquid homogenously and fast enough.
Economic Advantages and Flexibility Additional to the technical advantages there are obvious economic advantages with this new Conti-TDS-technology as well. The production costs of paint are typically reduced to below 10% compared to the dissolver process. Additionally, a significant reduction in raw materials is possible because of better dispersion, higher color strength and less thickener demand. A reduction of the production times to below 20% is typical. Consequently, energy savings down below 35% are reported as well. Generally the Conti-TDS guarantees higher product quality, much higher flexibility in the production and a much higher level of safety. The foot print of a Conti-TDS system is just some square meters. Because of the much faster process one Conti-TDS can always replace a number of dissolvers – on a very small space. Investment costs are much lower. For a new installation the investment costs are about 60% lower compared to conventional dissolvers. The return of investment is often shorter than 6 months. Another advantage is the short realization time: Normally it takes just between half a year and one year from the decision to the production. Today flexibility is getting more and more important. With such a system it’s possible to produce very effectively different formulations and variable batch sizes. Because of the compact design it is easy to expand the capacity if required in future. Since the machine is working independently from the vessel size it is possible to enlarge the process tanks in future if required. Therefore just the process tanks and their mixers are exchanged – nothing else. The core of the system – the Conti-TDS and the automatic control - remains untouched. The machines are already used in all fields of the industry in an extremely wide field of applications. All types of products, all viscosity ranges and all types of raw materials are processed. If there are completely new demands in future it is easy to restructure the process. The final product quality of the produced lacquers and paints is at least equal, in most cases are better than using traditional dissolvers.
| 當(dāng)生產(chǎn)還在一臺循環(huán)罐中進(jìn)行時(shí),另一臺循環(huán)罐已排空上一個(gè)批量并完成下一個(gè)批量液體的加料。粉料吸入結(jié)束后的平均50秒內(nèi),所要求的粒徑已達(dá)到且產(chǎn)品已準(zhǔn)備好轉(zhuǎn)移。當(dāng)本批量的產(chǎn)品準(zhǔn)備排料時(shí),機(jī)器自動(dòng)切換至第二臺循環(huán)罐開始生產(chǎn),如此只用一臺機(jī)器就可達(dá)到每小時(shí)生產(chǎn)20’000kg的成品涂料,即便是以連續(xù)不間斷的方式生產(chǎn)。
所有的Conti-TDS系統(tǒng)都有經(jīng)涂料行業(yè)證實(shí)的集成的自動(dòng)清洗裝置。為了保持工藝系統(tǒng)的潔凈,每個(gè)批量都包含一個(gè)清洗步驟。配方中的部分液體通過清洗噴頭加入,保持循環(huán)罐和所有相關(guān)部件的清潔。即使下一批是相同的產(chǎn)品,循環(huán)罐也會(huì)被自動(dòng)清洗。如有不兼容的原料或在不同顏色之間進(jìn)行產(chǎn)品更換,則可以追加液體進(jìn)一步清洗。
工藝罐內(nèi)裝有高效的捷流混合器,它能垂直推動(dòng)和上下轉(zhuǎn)動(dòng)液體。這些混合器起到瞬間均混的作用。這一作用非常重要,因?yàn)榉哿鲜歉咚傥氲?。以水平方向旋轉(zhuǎn)為主的簡單攪拌器不能做到均勻混合的,也不足夠快。
經(jīng)濟(jì)優(yōu)勢和靈活性 除了技術(shù)優(yōu)勢外,新型的Conti-TDS技術(shù)也具有明顯的經(jīng)濟(jì)優(yōu)勢。與高速分散機(jī)工藝相比,涂料的生產(chǎn)成本通常降低到10%以下。此外因?yàn)楦玫姆稚ⅰ⒏叩闹珡?qiáng)度和需要的增稠劑更少,可顯著減少原料用量。典型的是將生產(chǎn)時(shí)間縮短到原來的20%以下。據(jù)用戶的報(bào)告能耗節(jié)省至不到原來的35%. 通常Conti-TDS保證達(dá)到更高的產(chǎn)品質(zhì)量、更高的生產(chǎn)靈活性和更高的安全水平。 一臺Conti-TDS的占地面積只有幾平方米。由于更快的加工速度,一臺Conti-TDS 能夠在非常小的空間上替代好幾臺高速分散機(jī)。
投資費(fèi)用相對低許多。對于一條新的裝置,與幾套傳統(tǒng)高速分散機(jī)相比,投資成本大約不到其60%。投資回報(bào)一般不超過6個(gè)月。另一個(gè)優(yōu)點(diǎn)是項(xiàng)目建成時(shí)間短:通常從決定到投產(chǎn)運(yùn)行只需要半年到一年的時(shí)間。 今天靈活性越來越重要。采用這樣的系統(tǒng),可以非常有效地生產(chǎn)不同配方的產(chǎn)品和各種大小的批量。由于設(shè)計(jì)緊湊,很容易實(shí)現(xiàn)未來擴(kuò)產(chǎn)的需要。
由于機(jī)器的操作不受工藝罐大小的局限,可根據(jù)未來需要擴(kuò)大工藝罐,只需更換工藝罐和罐內(nèi)的混合器,再無其它,而裝置的核心機(jī)器 Conti-TDS及自動(dòng)控制系統(tǒng) – 維持不變。
該系列機(jī)器已在各行各領(lǐng)域中得到了極為廣泛的應(yīng)用。所有類型的產(chǎn)品、所有粘度范圍和各類型的原料都被加工過。如果未來出現(xiàn)全新的需求,工藝的重組也很容易。 生產(chǎn)的油漆和涂料的成品至少能達(dá)到相同的質(zhì)量,絕大多數(shù)情況下比傳統(tǒng)高速分散機(jī)所達(dá)到的質(zhì)量更好。 |
Dr.-Ing. Hans-Joachim Jacob, Process- and Application Engineering
Hans-Joachim Jacob工程學(xué)博士,工藝與應(yīng)用工程
· Studies at the Dresden University of Technology 1981 to 1986 in Mechanical Engineering
1981至1986年就讀德雷斯頓技術(shù)大學(xué)機(jī)械工程
· Since 1990 at the company ystral gmbh maschinenbau + processtechnik
自1990年 就職于德國ystral公司機(jī)械制造工藝+過程技術(shù)部
· Senior process engineer and customer application specialist
高級工藝工程師及客戶應(yīng)用專家
· Special expertise: Mixing, Emulsifying and Powder dispersion into liquids
專業(yè)知識:混合、乳化劑及粉體在液體中分散
如想了解更多請聯(lián)系:
伊思創(chuàng)(北京)工藝技術(shù)有限公司
北京市朝陽區(qū)東三環(huán)北路8號亮馬河大廈二座7層706室, 100004
For more information pls contact:
Ystral (Beijing) Process Technology Co., Ltd.
Landmark Tower 2, Unit 0706, 8 North Dongsanhuan Road
Chaoyang District, Beijing 100004 P.R. China
Phone: +86-10 6501 8070
Mobile: 13811270857
Email: ystral.china@ystral.com
www.ystral.com
相關(guān)產(chǎn)品
更多
相關(guān)文章
更多
技術(shù)文章
2022-01-05虛擬號將在 秒后失效
使用微信掃碼撥號